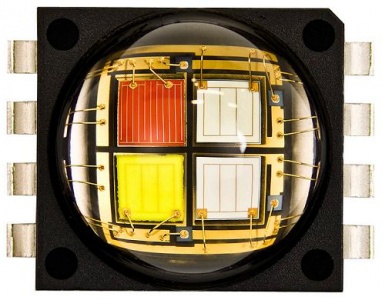
Queste note applicative descrivono una tecnica per la progettazione a basso costo di circuiti stampati (PCB) che ottimizzano il layout per il trasferimento di calore del LED, in particolare LED XLamp della CREE
La tecnica prevede l'utilizzo di supporto PCB tipo FR4, che costa meno, ma ha una maggiore resistenza termica rispetto a quelli con base metallica (MCPCB). L'utilizzo di fori rivestiti di metallo (fori metallizzati) dove appoggia il contatto termico del LED è un metodo per dissipare il calore attraverso un PCB-FR-4 appoggiato su un dissipatore di calore adeguato.
La tecnica dei fori metallizzati è utilizzata da Cree per i contenitori dei suoi XLamp LED elettricamente isolati.
Per la progettazione di alcuni sistemi di illuminazione, i fori metallizzati a conduzione termica permettono l'uso di circuiti stampati in FR-4 su schede che sono poi messe a contatto del metallo di dissipazione del calore generato dal LED.
Questa nota applicativa serve come guida pratica basata sui fondamentali principi di scambio termico e comprende la simulazione e misurazione dei dati relativi. Cree è un sostenitore di questa tecnica come design appropriato per alcune applicazioni di illuminazione e incoraggia i clienti Cree a prendere in considerazione queste tecniche disponibili per la gestione termica.
2. La gestione termica
2,1 XLamp Caratteristiche termiche
Tutti i contenitori (package) XLamp LED hanno un contatto termico isolato elettricamente, sia dall'anodo che dal catodo del LED, la cui superficie ottimizza il trasferimento di calore, inoltre il bordo del contatto può essere saldato o fissato direttamente a lato.
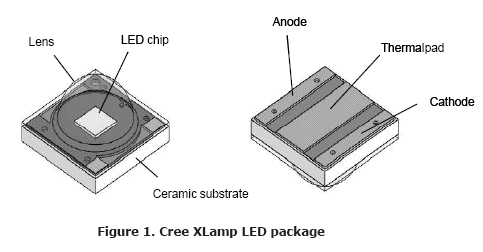
Il calore è condotto dal pacchetto LED attraverso il contatto termico del circuito stampato che dovrà essere montato su un adeguato dissipatore in modo da disperdere, in ambiente operativo, il calore prodotto.
La seguente tabella elenca i valori tipici di resistenza termica tra giunzione e punto di saldatura per i vari LED della serie XLamp.

2,2 caratteristiche termiche dei PCB in FR-4
Il laminato FR-4 è il materiale più comunemente utilizzato per realizzare i PCB e rispetta le direttive NEMA come ritardante di fiamma, è infatti un composto di fibra di vetro rinforzata con resina epossidica.
Tale prodotto ha però una bassa conduttività termica.
La Figura 2 che segue mostra una sezione trasversale tipica di un doppio strato di laminato FR-4.
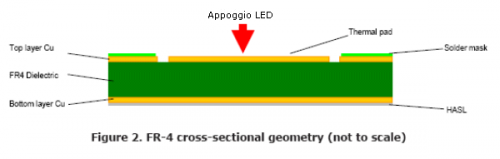
Utilizzando i valori di conduttività termica della tabella 1 , la resistenza termica totale di una scheda FR-4 può essere caratterizzata sommando le resistenze termiche per ciascuno degli strati.
θPCB = θlayer1 + θlayer2 + …+ θlayer3 ... + θlayerN
Per un dato livello è data la resistenza termica secondo la formula:
θ = l / (K x A)
(si assume un dissipatore di calore teoricamente infinita che mantiene il lato posteriore della scheda a 25 º C.)
dove l è lo spessore dello strato, K è la conducibilità termica, e A è l'area normale alla fonte di calore. Si consiglia di usare 1.6 mm di spessore con una superficie di circa 270 mm quadri, la resistenza attraverso il piano-termico è di circa 30 º C / W.
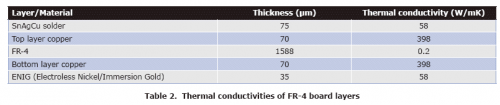
Circuito stampato tipo Metal-Core
MCPCB a semplice strato ha 4 livelli: la maschera di saldatura, lo strato di rame del circuito termicamente conduttivi e strato dielettrico, il tutto su un supporto di base fatto di metallo, come illustrato di seguito in Figura 3.
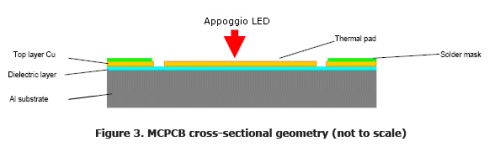
Utilizzando i valori di conduttività termica nella tabella 3, la resistenza termica
tra piano d’appoggio del led e il substrato di metallo della scheda è di circa 0,2 ° C / W.
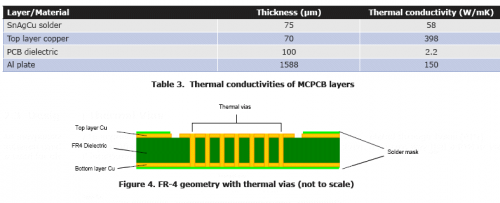
2,3 Progettazione termica attraverso fori metallizzati
Un modo economico per migliorare il trasferimento termico per PCB FR-4 è quello di aggiungere fori metallizzati passanti (PTH) tra gli strati conduttivi (fig.4). Questi contatti termici passanti sono creati da fori metallizzati, allo stesso modo utilizzato per le interconnessioni elettriche fra gli strati dei normali PCB.
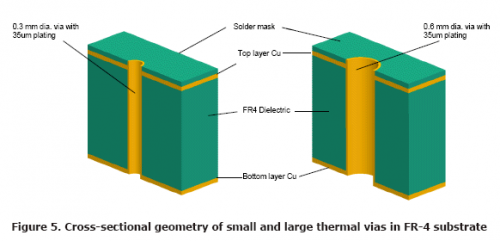
L’aggiunta di questi contatti passanti in modo adeguato fa migliorare la resistenza termica di uno stampato in FR-4. La resistenza termica di un foro passante può essere calcolata con la stessa formula:
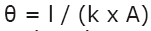
In base ai valori indicati nella tabella 4, per un solo passante del diametro di 0,6 mm risulta

Quando sono N passanti si ha:
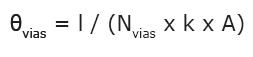
Questo è applicabile solo se la fonte di calore è direttamente a contatto con i fori passanti, in caso contrario, la resistenza aumenterà a causa di effetti di diffusione termica. Dovrebbe essere determinato, la resistenza termica totale per la regione sotto il contatto termico del LED, la resistenza termica equivalente per lo strato dielettrico e per fori passanti. Per semplicità, le due resistenze sono trattate come in parallelo applicando questa formula

Utilizzando i valori in tabella 4, con 270 mm quadrati si superficie con 5 fori passanti da 0,6 millimetri di diametro si ha una resistenza termica approssimata di 12 º C / W, un 250% di miglioramento rispetto ai 30 ° C / W derivata dai dati riportati nella tabella 2.
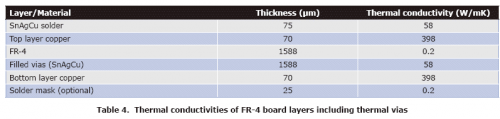
2,4 Foro passante aperto o riempito
I fori passanti vuoti portano a una resistenza termica superiore rispetto a quelli pieni perché la fonte di calore trova un’area ridotta per la formula
A =n x (D x t – t2)
dove D è il diametro del foro, t è lo spessore di placcatura e n pigreco.
Per un diametro di 0,6 mm di via con 35 micrometri di placcatura in rame, la superficie (normale al contatto termico) si trova a solo 0,06 millimetri quadri rispetto ai 0,28 millimetri quadri per un foro pieno, causando una resistenza termica di 441 º C / W per passante rispetto a 96,8 º C / W.
Per la stessa scheda di dimensioni e numero di passanti come nell'esempio precedente, il risultato attraverso il piano-termico la resistenza termica diventa 28 ° C / W.
Tuttavia, la capacità di creare passanti pieni e solidi in rame riduce ulteriormente la resistenza termica, rispetto al passante pieno di saldatura SnAgCu.
In generale, l'aumento dello spessore di placcatura durante la produzione del PCB migliorerà la resistenza termica del passante.
I fori passanti possono diventare pieni durante il flusso di saldatura ma se questo avviene non può avvenire in modo affidabile.
I passanti, se non sono riempiti in maniera affidabile, non sono uno strumento efficace per la conduzione del calore.
Un altro modo più sicuro ed efficace è creare un foro solido durante il processo di placcatura in produzione di PCB, oppure è quella di riempire il passanti con del rame (o qualche altro materiale termicamente conduttivi come la pasta epossidica conduttiva).
Fori passanti PTH vuoti
Figura 6a mostra un esempio di passanti parzialmente riempiti di saldatura , e la figura 6b mostra un esempio di saldatura con dei vuoti sotto il dispositivo (mostrato in rosso).
I vuoti aumenteranno la resistenza termica dell’interfaccia di dissipazione.
Inoltre, la saldatura può riempire eccessivamente il foro che può ridurre l'area di contatto tra il LED e dissipatore di calore.
Un modo per evitare questo è quello di mantenere una via di diametro più piccolo di 0.3 mm.
Lo svantaggio di questo approccio è che, con i piccoli fori passanti vuoti, porterà a una maggiore resistenza termica complessiva.
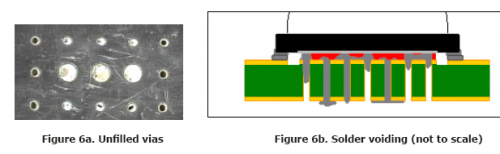
Un'altra tecnica per limitare l'assorbimento della saldatura sul lato inferiore comporta l'uso di una maschera per limitare il flusso di saldatura dal lato superiore del circuito stampato. Un processo, chiamato "a tenda", utilizza una maschera di saldatura per evitare che entri lo stagno sia in entrata che in uscita del foro passante termico, a seconda della parte a cui la maschera di saldatura è collocata. La tecnica con maschera di saldatura a Tenda sul lato inferiore per coprire il passanti termici può impedire allo stagno di scorrere giù nel foro e sulla parte inferiore della scheda. Nella top-side dei fori a tenda, sono disposti piccole aree di solder mask sopra i fori passanti dal lato superiore del PCB per evitare che dello stagno scenda nel passante dal lato superiore della scheda.
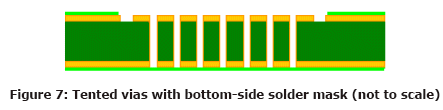
Fori passanti pieni
In generale, la creazione di fori passanti pieni in rame è in pratica una efficace tecnica preferibile.
Continua domani.....
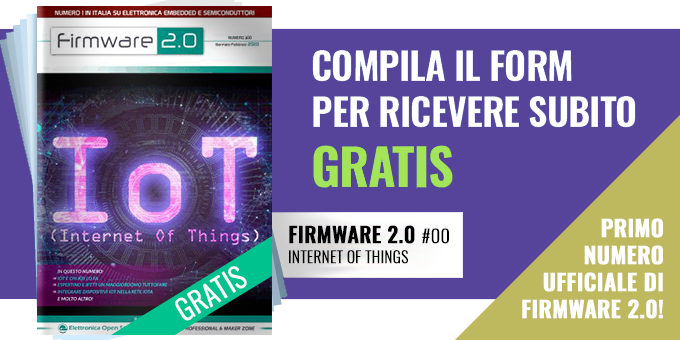
Ciao Vittorio, questa tematica è davvero interessante..soprattutto per chi si occupa di fare il layout delle PCB..Proprio in questi giorni mi son imbattuto nelle nuove tecniche di saldatura e perciò volevo chiederti una cosa :
In vista dell’arrivo della normativa RoHS (rinviato da un pò di anni ma dovrebbe entrare in vigore nel 2013/14) ho visto in giro che ci sono le cosiddette tecniche di saldatura “lead free” oppure le wave soldering… sai se in italia ci sono aziende che le usano già?
Le leghe che vengono utilizzate sono prive di piombo ma sono leghe SAC (stagno argento s Cu,oro) giusto? Sapresti dirmi qualcosa in più in merito a ciò? o fornirmi qualche esempio di processo già implementato?
Ovviamente estendo le domande a tutti 🙂
Veramente già da alcuni anni sia lo stagno che i circuiti stampati sono RoHS.
Praticamente lo stagno, il famoso 60/40 è ormai fuorilegge,
il piombo è stato sostituito dall’argento, in percentuale minore ovviamente 🙂
Ed anche i produttori di circuiti stampati non utilizzano più piombo nei circuiti
(almeno quelli dove mi fornisco io)
Vedi anche
http://it.emcelettronica.com/campionatura-di-circuiti-stampati-gratuita-da-cmt
Si si lo so.. ma se vedi qui ci sono state dei cambiamenti ed è stata emanata una nuova direttiva :
http://www.anie.it/browse.asp?goto=1198&IdDocumento=38241&IdRevisione=83482
che dovrà essere recepita entro 18 mesi da luglio di quest’anno.. Se vedi la direttiva alcune cose sono state tolte ed altre aggiunte..
Questa azienda ad esempio
http://www.servizi-elettronici.com/sun_electronics/Presentazione_SunElectronics.pdf
Altri link attienti all’argoemnto
http://it.emcelettronica.com/saldatura-senza-piombo-direttiva-rohs-33
http://www.okinternational.it/artec.html
http://web.tiscalinet.it/DarkMoon/files/Comparazione%20tra%20SAC%20e%20SN100Ni.pdf
http://www.prodelecgroup.com/ita/download/20090114-1063-PCB%20gennaio%202009%20Saldatura%20lead-free%20la%20sperimentazione%20continua.pdf
http://www.cabelpiu.it/user/File/Varie/FAQ%20SN100C.pdf
preso da questo asito http://www.cabelpiu.it/
E’ un articolo semplicemente fantastico!!! Hai fatto un ottimo lavoro, molto ben documentato ed estramamente istruttivo.
Sentitamente grazie,
Ciro.
e questa è solo la prima parte 🙂
sabato e lunedi le altre parti dell’articolo sull’ottimizzazione dei PCB per una corretta dissipazione termica dei led Cree Xlamp (ma anche led di potenza in generale)
Il meglio pare siano i fori ripieni di rame, riempiti al momento della creazione del PCB.
La lega saldante soprattutto se non penetra equamente non è il metodo migliore
a quel punto meglio fori metallizzati vuoti.
La base metallica del LED deve appoggiare in modo sicuro e con aderenza al PCB per poter smaltire bene il calore altrimenti se si creano leggere sporgenze di lega saldante la dissipazione diventa poco efficiente e il LED avrà vita breve.
Tieni d’occhio che a giorni uscirà un articolo che spiega come realizzare dei lampadari a ciondolo dove un certo tipo di LED appoggia sul supporto del lampadario fatto di alluminio tornito ad anelli per aumentare la dissipazione.
Vittorio,
non posso che aggiungermi ai complimenti per questa serie di articoli teorico/pratici molto ben fatti, e soprattutto utili in un campo, quello dell’illuminazione a LED ad alta potenza, ormai sempre piu’ in espansione.
Ho diversi amici che operano nel settore Architettura di interni che mi chiedono da modesto esperto di elettronica suggerimenti tecnici su questa o quella tecnologia per l’illuminazione. Credo che con questi articoli potro’ dare molte piu’ informazioni, attendo quello che stai preparando sul lampadario “ipertecnologico”, uno dei temi caldi che ogni tanto mi trova coinvolto.
In questi articoli di mio c’è assai poco.
Ho solo fatto una modesta traduzione di artcioli dela Cree ® intuendo che sarebbero potuti servire.
Penso che una buona dissipazione, anche se poi il PCB costa un po’ di più, allunga la vita del led pertanto ne vale la pensa
Si, a suo tempo 🙂
http://it.emcelettronica.com/m…