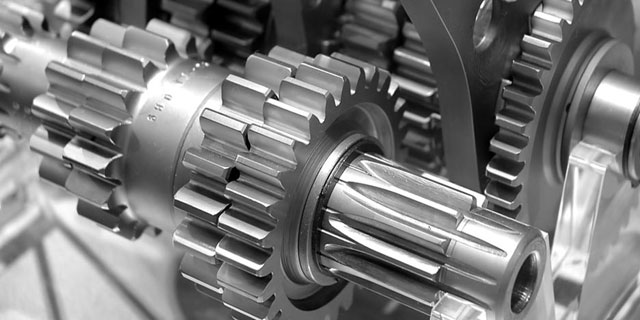
Prosegue l'arduo ed emozionante tour nell'assemblaggio della 3DRag, la stampante 3D Open Source made in Italy! È la volta della parte meccanica, con il montaggio e la messa a punto di tutta la "carrozzeria" prima dell'arrivo dell'elettronica ad animare l'intero sistema. Se vi è piaciuto lo scorso articolo, seguiteci anche in questo: ne vedrete delle belle....
La scorsa puntata abbiamo dato uno sguardo d'insieme alla stampa 3D: che cos'è, come funziona e di quali materiali si avvale.
In particolare ci siamo soffermati sulla tecnica del FFF (Fused Filament Fabrication), essendo quella su cui si basa la stampante di riferimento in questi articoli, la 3DRag. Infine abbiamo visto una panoramica di quest'ultima, cominciando a familiarizzare con alcuni dei pezzi che la compongono e le primissime fasi del montaggio (ci eravamo lasciati con il carrello "X" montato...).
Da questa puntata entriamo nel vivo dell'assemblaggio, proseguendo con la struttura metallica ed inserendo tutte le componenti meccaniche del sistema. Armatevi dunque di cacciaviti, olio lubrificante e tanta, tanta pazienza, poichè per gli "elettronici puri" questa parte potrebbe risultare meno coinvolgente.
Tuttavia, come accennato la volta scorsa, questi articoli non vanno presi come "istruzioni operative di montaggio" (per quello ci sono i vari wiki citati nel primo articolo) quanto piuttosto come un resoconto a macro-step delle esperienze di montaggio, dai flop ai piccoli successi collezionati. Insomma, il già citato "diario di viaggio" che magari potrà facilitare un pò la vita a chi deciderà di gettarsi dopo di me in questa esperienza.
Dovete sapere che...
- Potete montare la stampante 3D con i classici attrezzi normalmente presenti in casa, come brugole, cacciaviti, metro flessibile etc ma dotarsi di strumenti più specifici semplifica il compito (es. chiavi a bussola, calibro, squadretta a cappello, lima) .
- La precisione è FONDAMENTALE! Non stiamo lavorando con dei MEMS ma il montaggio di un sistema di questo tipo può comunque essere considerato un'operazione di meccanica di precisione. Specie nelle operazioni di allineamento barre e profili, non andate ad occhio e, se potete, usate un calibro digitale: il movimento dei carrelli lungo i tre assi deve risultare scorrevole e non frenato, altrimenti i motori micro-stepper fanno fatica e le stampe vengono sfalsate.
Struttura e dinamica
Una stampante di tipo RepRap è un connubio di elementi metallici e plastici, questi ultimi solitamente prodotti mediante un procedimento di stampa 3D stessa.
La struttura della 3DRag prevede anch'essa una serie di pezzi metallici, in parte in alluminio ed in parte in acciaio, ed una serie di minuterie plastiche in derlin quali ingranaggi, pulegge, cuscinetti, supporti, fine-corsa etc. prodotti mediante stampa ad iniezione).
La struttura portante è composta orizzontalmente da 4 profilati in alluminio (da circa 50 cm l'uno) uniti in modo da formare un quadrato, a cui si lega verticalmente un montante composto da 3 profilati uniti ad "U".
Rispetto all'impiego di metalli più densi, l'alluminio conferisce a questo scheletro una notevole leggerezza, che si paga tuttavia in termini di stabilità. Infatti, i movimenti motorizzati dei carrelli portano a vibrazioni degne di nota che possono riflettersi sulla qualità delle stampe, e pertanto risulta necessario che la stampante poggi su un tavolo massiccio e ben piantato a terra.
All'interno del riquadro orizzontale e parallelamente ad uno dei profili del montante verticale corrono delle barre d'acciaio (rettificate nel primo caso, filettate nel secondo), il cui scopo è quello di far scorrere i carrelli lungo un'unica direzione (rispettivamente, "X", "Y" e "Z"). In questo caso, dato che essi portano comunque un peso, la scelta di tale materiale è senz'altro più indicata dell'alluminio, che invece potrebbe, a lungo andare, portare a delle deformazioni. Una cosa che non mi stancherò di sottolineare in questi articoli è l'importanza di montare le coppie di barre di ogni singola direzione perfettamente parallele tra loro, onde evitare che lo scorrimento risulti forzato in certi punti.
A proposito di carrelli e loro scorrimento, vediamo di capire la dinamica dei movimenti della stampante, partendo dal componente montato la scorsa volta, il carrello "X".
Il carrello X è la piattaforma scorrevole che accoglie il piatto di stampa, ovvero il supporto sul quale viene depositato il materiale fuso dopo l'estrusione.
Si muove, per l'appunto, lungo la direzione X, quindi per intenderci, destra e sinistra.
L'intera piattaforma è a sua volta vincolata a muoversi lungo la direzione Y, quindi nord e sud. Ciò avviene mediante un altro carrello con cuscinetti che scorrono su barre rettificate, per l'appunto il carrello Y.
L'insieme di questi elementi vincolati dà luogo praticamente al movimento sul piano del piatto di stampa.
In ultimo abbiamo il carrello Z, su cui è montato il braccio con l'estrusore, che si muove solo lungo l'omonima direzione tramite una chiocciola, il che vuol dire che durante la stampa va sempre e solo dal basso verso l'alto (ricordate il workflow descritto? Si realizza una "fettina" del modello in basso e poi ci si alza di uno step per iniziare con la successiva).
Nel complesso, durante la stampa di una singola slice, il carrello Z (e dunque l'estrusore) rimane fermo, mentre c'è un continuo lavoro dei carrelli X ed Y, ed è il loro avvicendarsi nei movimenti che dà l'effettiva forma all'oggetto della stampa.
Ad ogni modo, un breve video vale più di mille parole.
Il montaggio della struttura è un pò lungo, soprattutto a causa della più volte citata necessità di allineare bene le guide ed i supporti agli elementi mobili. Tuttavia, salvo in qualche punto, non risulta particolarmente difficile.
A mio avviso, l'unica cosa davvero ostica è stato il posizionamento delle cinghie di trasmissione nei relativi pignoni e pulegge dei carrelli: non essendo componenti chiusi, si deve sistemare prima un tratto di cinghia a cavallo del pignone e poi l'altro tratto nella puleggia (o viceversa) dopodichè unire i lembi rimasti liberi e fermarli tramite una morsa in modo da formare un corpo unico. Operazione sia di forza che di precisione, piuttosto faticosa...
La lubrificazione dei cuscinetti e delle barre di scorrimento è fondamentale; tuttavia, consiglio fortemente di usare olio e non grasso. I movimenti devono risultare fluidi, non "pastosi", per questo uno dei comuni olii usati in casa per sbloccare le viti molto strette o vecchie è preferibile.
Ultima nota sulla struttura: è previsto che sul montante verticale del telaio venga posizionato il supporto per la bobina del materiale di stampa (ad es. il PLA).
Si tratta di una barra filettata nella quale, tramite rondelle e cuscinetti, si ricava lo spazio orizzontale di alloggiamento per la bobina: non è molto lunga e si presta bene ad ospitare bobine non eccessivamente capienti, diciamo fino ad un paio Kg circa di materiale. Per esperienza, una bobina (piena) da 2,3 Kg come quella descritta nel precedente articolo, tende ad incurvare sensibilmente la struttura ma senza portare problemi degni di nota.
I motori
I motori impiegati sono 4 stepper di tipo NEMA-17 prodotti dalla Wantai Motor, quadrifilari, da 3.1V DC e con assorbimento a massimo carico di 2,5A (in condizioni normali, ovvero ad una velocità di stampa di circa 120 mm/sec, l'assorbimento è di circa 1,25A).
La coppia erogata si attesta sui 0,5 Nm, non elevatissima tra i motori in ambito CNC ma più che sufficiente per il peso che devono spostare.
La loro caratteristica principale è l'accuratezza dello step, che porta ad avere una rotazione controllata di 1,8°.
Inoltre, l'azione combinata dei motori e dei cuscinetti a ricircolo di sfere impiegate nei carrelli, porta ad avere un'alta risoluzione di movimento (nel senso di step precisi), dell'ordine di 0,015 mm nelle direzioni X ed Y e di 0,39 micron nella Z.
Ogni asse di scorrimento ha il suo motore, comandato direttamente dalla scheda di controllo della stampante.
Il 4° motore è impiegato nel meccanismo di trazione del filamento verso l'estrusore, ed essendo tale dispositivo fissato al braccio Z dell'intera struttura, determina l'unico caso in cui un motore si muove durante la stampa (quelli dei carrelli X, Y, e Z restano tutti fermi).
L'estrusore e la ventola
L'estrusore è l'elemento nel quale il filamento di materiale utilizzato per la stampa viene disciolto per poi essere depositato.
In pratica si tratta di un sottosistema nel quale le parti fondamentali sono:
- l'elemento riscaldante con ugello di uscita;
- la ventola di raffreddamento;
- il condotto motorizzato di trazione del filamento;
Il meccanismo di estrusione impiegato nella 3DRag prevede un elemento riscaldante di tipo Wade con corpo in ottone ed ugello in acciaio, dotato di resistenza di potenza e in grado di superare i 250° C. Il riscaldamento ed il controllo della temperatura raggiunta (tramite sonda NTC in vetro presente nel corpo estrusore) avviene tramite la scheda elettronica della stampante, ed i valori si impostano direttamente via software. A mantenimento della temperatura raggiunta dall'ugello è posta una calza in fibra di vetro.
Al raffreddamento post-estrusione del materiale utilizzato è deputata una piccola ventola da 12 V DC da montare sul braccio Z della struttura mediante staffa in alluminio. Il ruolo di tale ventola assume un'importanza particolare nel caso di utilizzo del PLA, che in assenza di un flusso d'aria refrigerante tenderebbe a rimanere più a lungo in uno stato semi-fluido, portando quindi a deformazioni nella stampa.
Riguardo alla trazione del filamento, il condotto prevede un canale di scorrimento con foro di entrata da 3mm di diametro: l'azione del motore permette l'aggancio e la spinta del filo attraverso un cuscinetto ed una vite dentata, con conseguente ingresso dello stesso attraverso un canale in teflon. A questo punto il filo giunge al fusore in ottone, all'interno del quale viene disciolto e fatto fuoriuscire da un ugello con foro da 0,5 mmm .
F.A.Q.
Q. Quanto tempo richiede l'assemblaggio della parte meccanica?
A. Se avete due/tre ore di tempo libero al giorno, con una settimana ci si riesce.
Q. Con questa struttura, che dimensioni di stampa posso raggiungere?
A. Il lato positivo di avere una struttura (un pò) ingombrante come questa è la dimensione utile di stampa permessa. Si arriva a stampare oggetti fino a 20x20x20 cm, che per un uso domestico ed hobbystico non sono pochi.
Q. Questo tipo di componentistica permette di stampare con altri materiali oltre ad ABS e PLA?
A. La 3DRag si basa sulla tecnica FFF, per cui ogni tipo filamento che può essere disciolto e depositato va bene. In linea di massima, il parametro su cui si gioca è la temperatura di lavoro ed ogni materiale ha la propria. In commercio esistono già altri tipi di plastiche, nylon, addirittura compositi in fibra di legno...
Q. Quanto tempo ci vuole a fare una stampa?
A. Dipende dalla complessità dell'oggetto da stampare. In termini prestazionali, la velocità massima di deposizione del filamento disciolto è di 300 mm/s, il che si traduce in tempi che vanno da meno di un'ora per il classico fischietto (in pratica "l'Hello World!" nel campo della stampa 3D) ad alcune ore nel caso di geometrie complesse. Il tempo aumenta inoltre in base all'uso di specifiche opzioni di stampa quali ad esempio il "brim", ovvero il bordo di tenuta per il materiale da depositare sul piatto, e la densità di riempimento di ogni singola slice stampata.
Q. La precisione nell'assemblaggio è davvero così importante?
A. Purtroppo sì. Specie negli allineamenti delle barre di scorrimento. Immaginate cosa accadrebbe ad un treno in movimento se i binari su cui viaggia non fossero paralleli. Fortunatamente, però, le componenti meccaniche da montare sono già dotate di guide e vincoli, per cui una buona parte del lavoro di calibrazione ci viene risparmiato in partenza.
Conclusioni
Dal precedente articolo abbiamo fatto molta strada. Se osservate la scatola del kit di montaggio, adesso la si può finalmente guardare senza avere paura!
Senz'altro la parte di assemblaggio della meccanica è stata lunga ed impegnativa, ma alla fine, dopo ore di sonno perso ed a volte smontaggio e rimontaggio di qualche parte venuta male, ce l'abbiamo fatta.
Nel prossimo articolo ci occuperemo da vicino della parte elettronica (scheda, cablaggi, firmware e software di controllo) ed effettueremo le prime calibrazioni di tutto l'insieme dal PC. Di sicuro, per gli amanti dell'elettronica, una parte più intrigante.
Da un ammasso di ferraglia e fili, vedremo finalmente prendere vita qualcosa. Parafrasando uno spot TV degli anni '80: "Magia? No, tecnologia!"
Stay tuned!
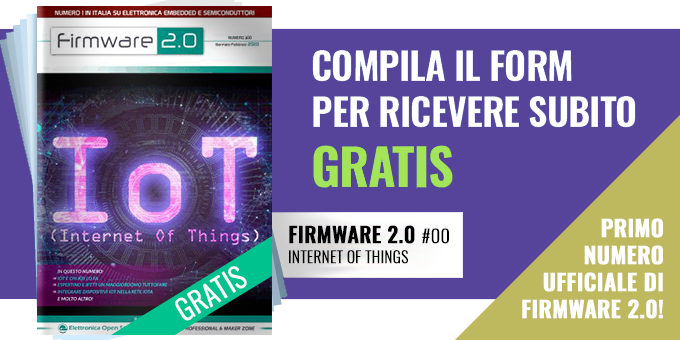
Questi articoli in stile “diario di un appassionato di tecnologia” stanno diventando veramente interessanti 😉
Sul firmware, in effetti, avrò di che chiedere…. 😀
Ottima pagina di Diario da Maker 😀
Anche io sono d’accordo con Piero che afferma che questi articoli fatti con questo stile stanno diventando davvero interessanti, perciò ti faccio i miei Complimenti, specialmente per la spiegazione e le foto “passo passo” che aiutano sicuramente a comprendere meglio qual’è il funzionamento una stampante 3D e più nello specifico quale è lo scopo di ogni parte (Hai detto anche che a mantenimento della temperatura raggiunta dall’ugello è posta una calza in fibra di vetro :D).
Ricordo quando ho letto il primo articolo di questa serie nel quale hai affermato:
”
Quando mi è arrivata a casa, una volta aperto il pacco mi sono messo le mani nei capelli: più di 40 buste di pezzi meccanici ed elettronici!
”
Bhè… devo dire che ti sei sbracciato e messo all’opera visto il risultato che hai ottenuto, hai eseguito davvero un ottimo lavoro e spero di leggere presto la parta che riguarda l’harware e il software.
A presto,
Ivan.
Ti ringrazio 🙂
Di scritti “seri” e teorici sull’argomento ce ne sono in giro diversi…
In effetti volevo dare al resoconto una forma a cavallo tra la divulgazione formale e qualcosa di un pò personalizzato…e mi è venuto in mente lo stile del diario.
E, dato che i tempi di realizzazione non sono stati poi così brevi, il diario in questione si avvicina molto a quello di un viaggio: la partenza è stata la scatola “con le mie mani nei capelli” e l’arrivo sarà il veder nascere la prima stampa.
Ovviamente senza che quest’ultima sia da ritenersi una meta definitiva, ma soltanto una prima milestone.
Il bello di un viaggio così poco “strutturato” è, a mio parere, il fatto che esattamente non so come si svolgerà da qui in avanti (in realtà nel momento in cui scrivo questo commento ho terminato i cablaggi elettrici…): ma mi piace pensarla un pò alla Jack Kerouac:”-Dobbiamo andare e non fermarci finché non siamo arrivati.- -Dove andiamo?- -Non lo so, ma dobbiamo andare-“.
Grazie mille Ivan,
in effetti di lavoro ce n’è stato, e non ti nascondo che quando ho scattato l’ultima foto di questo articolo ero abbastanza contento: finalmente la scatola VUOTA!!!
La parte meccanica, per quanto meno appassionante per un elettronico, è quella che comunque fa (o dovrebbe far) capire più nei dettagli come lavora una stampante 3D, perlomeno come funzionano i suoi “muscoli” (di alluminio…).
Spero di potervi fornire una simile quantità di dettagli anche quando parlerò della sezione elettronica/informatica: vi anticipo solo che, una volta cablato il tutto, il grosso del lavoro si sposta “in fretta” da viti e bulloni (che rivedremo solo per settare i vari fine-corsa elettromeccanici) alle operazioni sul PC, con una buona dose di parametri da calibrare ed impostare.
Personalmente è la parte che preferisco: quando vedo la pressione di un tasto sul computer che diventa il movimento di un motore su un sistema CNC mi sento meglio… 😉
Bellissimo, ben spiegato e ben documentato con foto che rendono l’idea di cosa si cela dietro ad un montaggio del genere (che non è per niente semplice se non si ha la giusta dose di calma e pazienza).
Guardando le foto noto che assomiglia tantissimo alla fresatrice per metalli che ho costruito qualche anno fa (costruendo al tornio per metalli i vari pezzi critici), il telaio è di alluminio pieno da 1,5 cm di spessore mentre questa utilizza lo scatolato, l’altra differenza è che i movimenti x, y e z da me sono manuali, si utilizzano tre volantini (in futuro penserò a “cncizzarla”).
Leggendo l’articolo mi è venuto in mente che basta sostituire il motore/mandrino con una testa scaldante (dopo averla motorizzata ovviamente) e diventerebbe una stampante 3D.
Ancora complimenti, aspetto la continuazione perchè è più che interessante.
Ciao
Mario
Ciao Marven
La tua idea di trasformazione della 3Drag in una stampante CNC corretta, e se vuoi saperlo l’idea è già venuta ad altri.
Infatti, se vedi sul blog della Futura elettronica, puoi vedere come hanno modificando la struttura della 3Drag hanno strasformato la stampante per plastica in una piccola CNC.
Come hai proposto hanno sostituito l’estrusore, che è stato semplicemente spostato, con un elettroutensile, tipo Dremel o Proxxon.
In quest’applicazione la 3Drag è utilizzata per realizzare circuiti stampati, è bisogna dire che se le foto sono veritiere la qualità è ottima.
Puoi avere maggiori informazioni a questo link.
http://blog.elettronicain.it/2013/11/14/realizza-i-tuoi-stampati-con-la-3drag/
Mentre è possibile vedere la macchina al lavoro visionando questo video.
http://youtu.be/-I7zFPLiKr8
Saluti
Adriano
Leggendo questo secondo articolo non si può che essere d’accordo con il coro di complimenti, anch’io apprezzo come ha detto Ivan il fatto di avere inserito nell’articolo le foto della realizzazione.
Non mi piacciono molto gli articoli, dove è descritto un progetto ma dove si vedono poche foto, schemi e figure.
Spero, tra l’altro, a fine lavoro di vedere anche qualche tuo filmato che illustri la realizzazione di qualche modello 3D.
Adesso passerai alla parte elettronica, per cui hai davanti altre puntate.
Per quanto riguarda la parte elettronica, credo che tu sappia, e sarai sicuramente informato che la rivista Elettronica In ha realizzato una scheda che permette di controllare senza PC la 3Drag, stampando i modelli grazie al fatto che la board è dotata di un lettore di SD card in cui inserire una scheda di memoria dove caricare i file da stampare. L’articolo è presente sul numero di Giugno 2013
http://www.elettronicain.it/myMain/riviste/p_rivista.asp?nrRivista=EI177&tipo=edicola
Tra l’altro sul numero di Luglio è stato pubblicato un articolo con le istruzioni per realizzare il contenitore per la scheda da far realizzare alla 3Drag stessa.
http://www.elettronicain.it/myMain/riviste/p_rivista.asp?nrRivista=EI178&tipo=edicola
Per quanto riguarda eventuali problemi o richieste, la rivista ha un Forum specifico sulla macchina.
http://forum.futurashop.it/viewforum.php?f=67&sid=5bd0f3cbf565093fa3394befed55bc05
Saluti
Adriano
Grazie per i cmplimenti Adriano!
Le foto passo passo secondo me sono un must in questo tipo di divulgazioni: inserire foto del tipo prima/dopo (stile pubblicità dei prodotti dimagranti 😉 ) non danno l’idea del lavoro che c’è dietro…
Cercherò di fare altrettanto con la parte elettronica, benchè in questo caso a fare da “modella” sia principalmente la scheda di controllo, oltre naturalmente ai vari cavi che vi arrivano.
Quando tratterò della messa a punto e prima stampa, farò in modo di inserire un video, così da far vedere “in tempo reale” cosa accade quando si lancia il comando di stampa.
In effetti ogni giorno che ho lavorato alla parte meccanica mi sono sempre piazzato la telecamera davanti ed ora ho collezionato ore di filmati “grezzi” (ovvero senza tagli sulle parti meno interessanti e senza filtri sulle parolacce durante i momenti di incxxxxtura…). Per motivi di tempo, non riuscirò a mettere su questi articoli quei video, ma il video finale della stampa ci sarà senz’altro.
Grazie per le fonti che mi hai segnalato. Quegli articoli li avevo letti in cartaceo (e non ti nascondo che stavo già facendo un pensiero alla scheda per il controllo autonomo della stampante…): probabilmente, dopo aver preso dimestichezza con qualche stampa di prova, realizzerò il case per la scheda di controllo. O magari sarà proprio su questo che realizzerò il video… 😉
Quanto alla segnalazione sul “porting” della 3DRag a macchina CNC per realizzare PCB, devo veramente ringraziarti di cuore. Mi piace molto la stampa 3D in generale ma il mondo CNC “classico” sinceramente è quello che preferisco!
Avevo motorizzato una fresatrice Proxxon MF70 e resa a tutti gli effetti una macchina CNC con scheda di controllo, ma sapere che anche la 3DRag può essere utile allo scopo fà molto comodo!
Cia Marven, grazie 🙂
Confermo: la pazienza serve davvero tanto 😉
Sono contento che che ti sia venuta in mente l’idea per “stampantizzare” la tua fresatrice. In effetti i mondi della stampa 3D e delle macchine CNC si intersecano molto (anzi, in teoria il primo deovrebbe essere un sottoinsieme del secondo…).
Spero, con i successivi articoli, di stuzzicare qualche altra idea…
Un saluto
Ottima soluzione! 🙂
grazie, come sempre hai qualche link utile da consigliare 😉
😉
grazie!